Supply chains are the bloodline of modern economies, and they wouldn’t exist if it weren’t for inbound and outbound logistics. Logistics support the movement of goods and services from origin to consumer. Within a supply chain, there are several processes, of which inbound and outbound logistics play a crucial role. Let's take a look at what inbound and outbound logistics are to help you understand where and how your company can make the best logistics solutions.
The Benefits of Logistics and Why It’s Important
Look at the objects surrounding you. The shoes you wear, the food you eat, and everything that’s around you got to you through a sophisticated logistics process. For consumers, the benefit of logistics is the acquisition of goods and services. For businesses, it’s competitive advantage and positive reputation management.
When outbound and inbound logistics align, they produce effective supply chains with increased efficiency and sales, as well as improved vendor and customer relationships. All facets of a company need to work together on both internal and external logistics to ensure business success.
Businesses tend to consider their supply chains to be a cost instead of a tool for driving added value and increased efficiency. Those that optimize their supply chains decrease overall inventory needs, reduce costs and improve throughput.
Benefits of Inbound Logistics
An efficient inbound logistics system is necessary for any business to ensure the uninterrupted flow of goods into its warehouse. It also provides the following:
- Improvements in shipment delivery times
- Increased customer satisfaction and trust
- Minimizes product damage potential
- Better inventory management
- Timely updates to mitigate disruptions
- Steady production rates
Benefits of Outbound Logistics
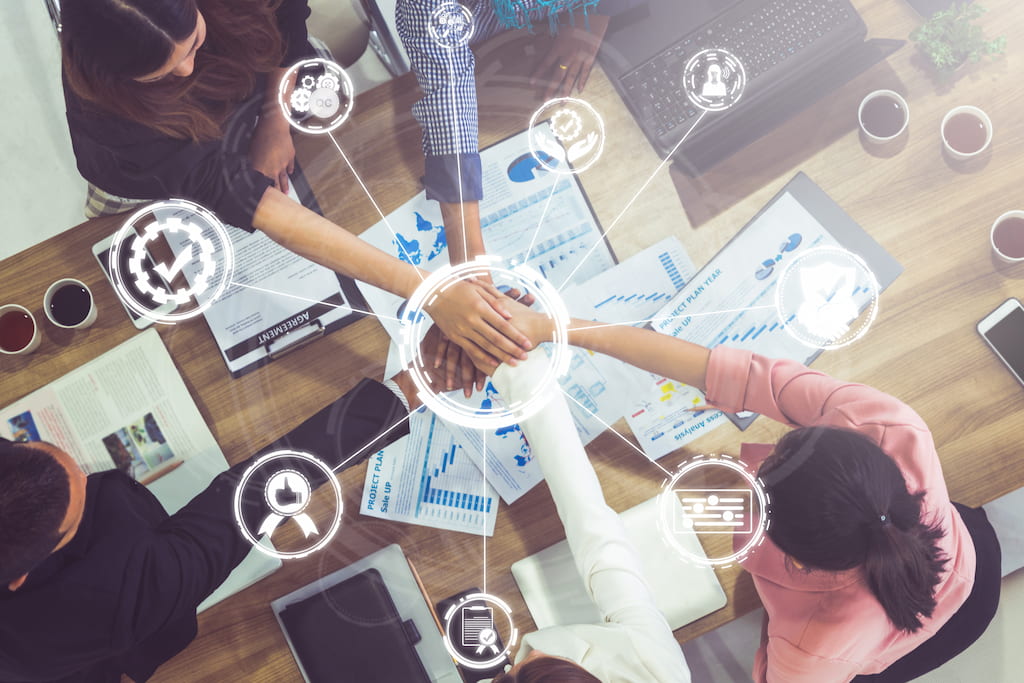
Outbound logistics is customer-centric, ensuring products and goods delivered on time are of a high-quality standard. The many benefits include:
- Faster deliveries that are on time
- Fewer cancellations
- Reduced delivery mistakes
- Improved customer satisfaction and loyalty
- Decreased returns
- Less transit damage
- Efficient business planning
- Reduced company and consumer costs
What Is Inbound Logistics?
At Cowtown Logistics Freight Management, we’re sometimes asked, “what does inbound logistics mean?” It is the receiving of raw materials from a supplier to a warehouse. This process includes ordering, receiving, storing, transporting, and managing incoming supplies. Goods travel from suppliers, manufacturers, and distributors to companies, retailers, or a third-party logistics company.
Inbound Logistics Operations
The handling of inbound logistics is company and industry-dependent. It usually entails the following operations:
- Purchasing & Sourcing: Identify potential suppliers, shopping around for quotes, and negotiating the best prices. It’s crucial for businesses to partner with a credible supplier to ensure inventory is optimally stocked.
- Purchasing: Calculating the correct quantities of materials needed, making a purchase, and ensuring the materials arrive on time.
- Transportation: Deciding whether materials will be shipped via boat, plane, or over-the-road. Factors like delivery speed, choice of carrier, ideal route, and transportation price for incoming supplies are considered.
- Receiving: Unloading trucks once materials arrive and ensuring the goods are delivered to match the order.
- Warehousing: Moving the goods from the receiving dock to their assigned warehouse locations.
- Inventory Management: Deciding on the type of materials you should store and why to locate them. Most companies have an inventory management system to help them keep track of product arrival and departure.
- Distribution: Sending goods to their destination inside the business.
- Tracking: Monitoring incoming order details, such as invoices, location, and delivery timeline.
- Reverse logistics: Bringing back goods from customers due to returns or delivery issues. These need to be examined and restocked into available inventory.
Inbound Logistics Process
The following processes have to occur for inbound logistics operations to take place:
- Purchasing & Sourcing: The company finds vendors that can supply the goods it needs, negotiates a price, and buys them.
- Recording & Sourcing: The company then records the purchase order (PO) and receives a receipt once it has made the payment.
- Notification: The supplier electronically notifies the company once it's shipped materials and provides shipment tracking information.
- Load Arrival: The goods arrive at the company’s docking facility.
- Receiving: Warehouse workers unload incoming goods and verify the quantity and condition before accepting the order. The goods are then moved to the manufacturing inventory at a factory or placed in a warehouse for later or at a staging point for cross-docking.
- Reverse Logistics: The receiving team handles products sent back from customers for returns or repair.
Inbound Logistics Challenges
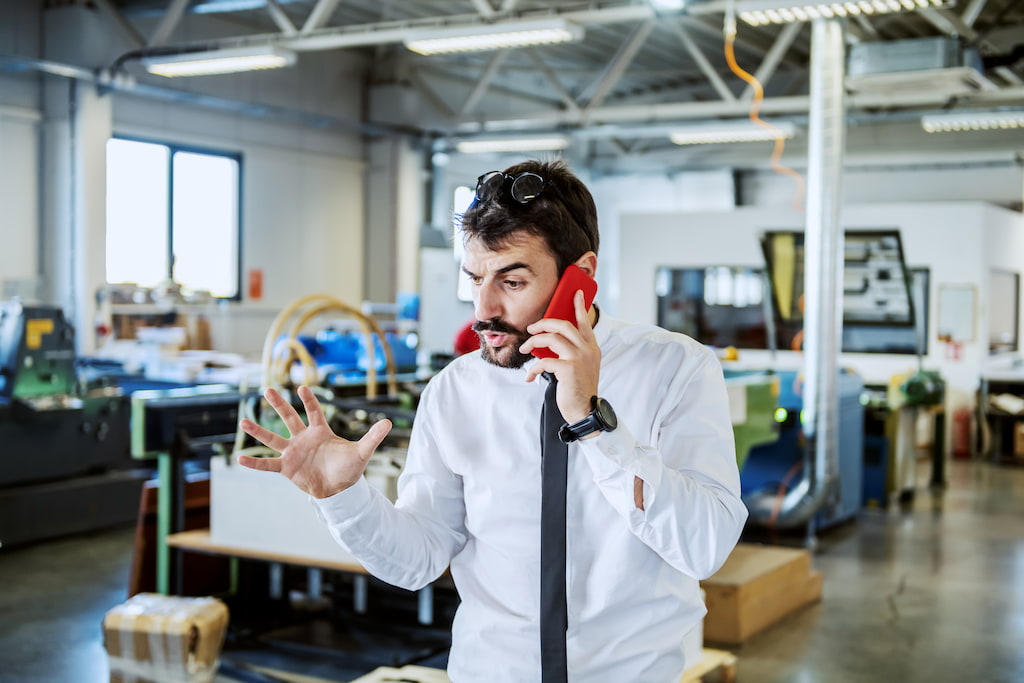
If you want to know how to improve inbound logistics, you need to look at combating common challenges like unreliable delivery and lead times,
- Shipping Inefficiencies: Sometimes, companies spend too much on shipping or don’t consolidate their loads properly.
- Lack of Information: When shippers don’t use real-time information systems, companies don’t have the data to make decisions. This leads to inventory mismanagement and production delays.
- Product Surges: Without planning, company’s can land up juggling too many deliveries at once, causing confusion and potential inventory mix-ups.
- Supply & Demand Balance: Not having sufficient data to balance your order pipeline.
Inbound Logistics Examples
Here’s an example of how inbound logistics processes and operations work for a home
linen company called Biggie Best.
- Purchasing & Sourcing: Biggie Best determines how much fabric it needs for this season’s linen ranges to meet forecast sales projections. Its procurement team works with designers to find components the company needs for the quantity, delivery date, and price. The purchasing manager will negotiate a contract with each vendor.
- Recording & Receipts: A procurement clerk will send purchase orders (POs) to suppliers and log them, ensuring they match with invoices and receipts.
- Notification: The vendors send electronic acknowledgments of the POs along with tracking information.
- Load arrival: Trucks with materials arrive at Biggie Best’s design facility.
- Receiving: Biggie Best’s staff unloads the materials and scans the barcodes to count and identify products. They quality-check the orders before moving them to a warehouse, where they’ll be turned into the bedding.
- Reverse Logistics: A Biggie Best receiving team handles unsold linen from retailers. Last season’s linen goes to a staging area for the team that handles discount store orders.
How to Improve Inbound Logistics?
To improve inbound logistics, you need to assess every touchpoint and process in order to streamline your supply chain:
- Measure Process and Performance: Measure the cost, waste, duplicate & low-quality work, communication gaps, and unnecessary delays. How much time, resources, and money is wasted?
- Scrutinize Choices: Does buying in bulk to receive a discount cost more in the long run? Are your supplier management choices efficient?
- Use the Right Warehouse Management System: This is essential for the entire process of inbound systems. Is yours easy to use? Does it enable streamline packing and reviewing? Can you set reorder points?
- Improve Supplier Relationships: All business is built upon good relationships. Having better relationships with suppliers and vendors will allow you to grow business trust and negotiate better deals.
- Implement a Transportation Management System (TMS): A TMS will provide you with the knowledge to make informed decisions about vendor quotes.
Benefits of Optimizing the Inbound Logistics
Managing your company’s inbound logistics processes isn’t just cost-efficient, it also significantly improves efficiency of the supply chain. The following are just a few of the benefits:
- Saving on freight costs: By looking more closely at your inbound logistics, you can locate opportunities for consolidation or rate reductions. Inbound logistics focuses on making your supply chain management strategy more efficient, which can save you big bucks in the long run!
- Driver-friendly: By consolidating and pooling your inbound orders, you also save truck drivers time and earn a reputation of being a driver-friendly company! Drivers will appreciate that you took the energy to prevent them from having to take unnecessary trips across towns and cities.
- Boost KPIs: The improvements you’ll see in costs, on-time deliveries and pick-ups, and technology demonstrate fantastic growth to supply chain partners.
- Better use of resources: A common inbound logistics example of waste occurs when members of your workforce spend valuable time waiting around to receive a load. Poor communication and planning results in easily preventable wasted labor.
- Increase visibility of the O2C: The Order-to-Cash Cycle, or “O2C” for short, is the cycle of raw goods becoming final sellable product, and it’s best to keep it as short as possible. By optimizing your inbound delivery process, you cut down on stalls in the cycle and get to the “cash” part more quickly.
- Reduce inventory requirements: When you know your company’s inbound logistics processes, you reduce your reliance on safety stock and keep your inventory at a manageable level.
What Is Outbound Logistics?
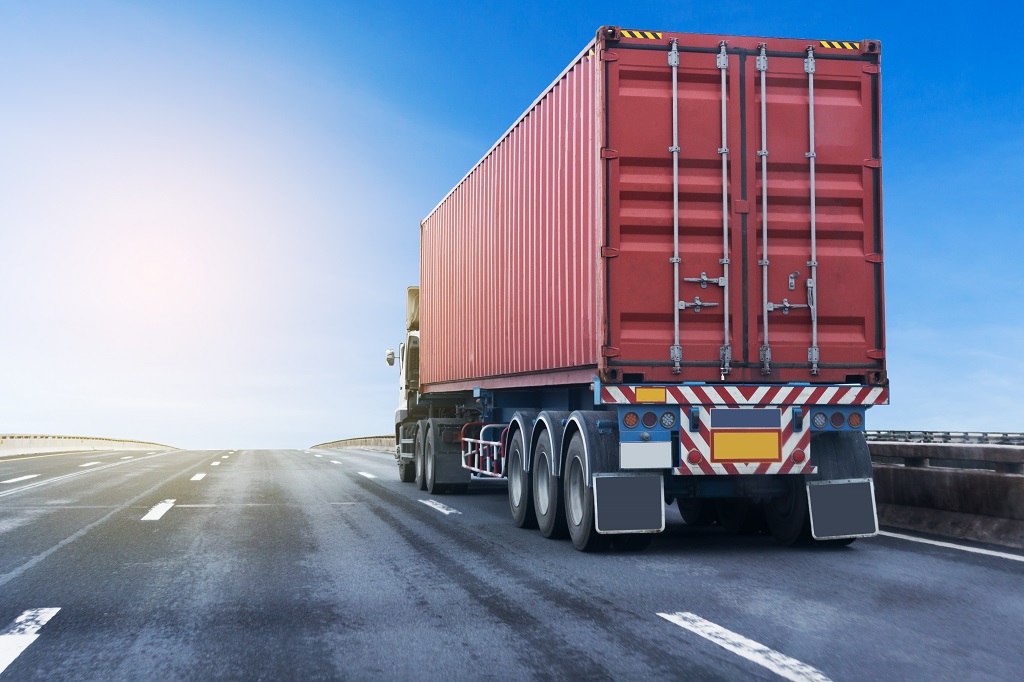
Similarly, we’re also sometimes asked, “What is the meaning of outbound logistics?” Outbound logistics is the process of getting final goods delivered to the consumer. It involves storing and moving goods to the end-user. Steps in this process include order fulfillment, packing, shipping, delivery, and customer service related to delivery. Goods travel from a company, brand, retailer, or third-party logistics provider to customers.
Outbound Logistics Operations
Like outbound shipping logistics, how a company handles outbound logistics is industry and product-dependent. The following operations usually comprise outbound logistics operations:
- Warehouse & Storage Management: Companies store a certain quantity of goods to meet consumer demand. Outbound logistics deals with outgoing finished products.
- Inventory Management: This includes tracking the type and number of orders and maintaining product quality through quality control assessments and measures.
- Transportation: Managing the mode of transportation dictated by the product and quantity.
- Delivery: Ensuring the timely delivery of the correct products to the consumer.
- Distribution Channels: Outbound logistics deals with the ways products reach consumers, whether it’s direct to consumer, through value-added resellers, dealer networks, or drop shipping, for example.
- Last-mile delivery: The last shipping leg before the product reaches the consumer and the most costly. Each delivery requires individual handling because it goes to a single address.
Outbound Logistics Process
The general outbound logistics process entails the following:
- Customer order: A customer places an order through a channel where a company sells its products.
- Order Processing: The company validates the order, receives the quantity and products from its inventory, and produces documentation.
- Replenishment: New inventory is moved to replace the purchased product. This may trigger the production of more materials to maintain optimal inventory levels.
- Picking: Warehouse workers pick the products to fulfill the order.
- Packing, Staging & Loading: Products are packaged according to customer needs and loaded onto outgoing trucks.
- Shipping & Documentation: As the order leaves the warehouse, the company’s system logs the shipment and sends tracking details to the customer.
- Last-Mile Delivery: The order is delivered to the customer.
Outbound Logistics Examples
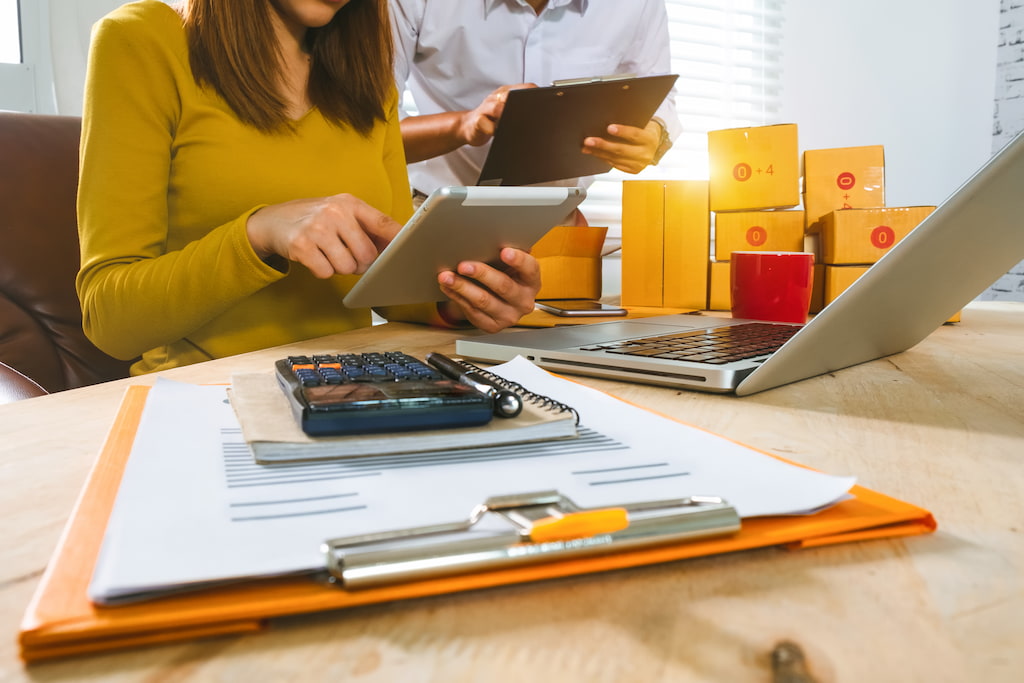
Here’s an example of how the outbound logistics process works for linen store Biggie Best.
- Customer Order: A large hotel chain orders new linen. The order is massive, but each hotel has a different number of rooms, so Biggie Best’s team needs to note carefully which orders belong to which hotel.
- Order Processing: The team checks they have the number of items for the order. They send a confirmation to the hotel chain. Biggie Best allocates these items in the warehouse, so they can’t be sold to another customer.
- Replenishment: Staff move the order from storage to the shipping warehouse and replace or reach out to vendors to make more linen.
- Packing, Staging, and Loading: When the linen reaches the packing area, staff scan barcodes to confirm it’s the correct order before loading it onto trucks.
- Shipping & Documentation: When the order departs, Biggie Best logs the shipment and sends tracking details to the hotel chain.
Outbound Logistics Challenges
If you want to know how to improve outbound logistics, you need to think about customer satisfaction and address issues related to incorrect deliveries.
- Operation Coordination: The logistics team needs to manage order surges. When production scales, more warehouse space is required, or goods need to reach customers faster. Meeting storage capacity and demand is a critical challenge.
- Inventory costs: Sometimes, companies don’t maintain enough inventory to accommodate customers’ changing demands, leading to a lack of stock or unnecessary holding costs.
- Transportation costs: If loads aren’t consolidated, more money than needed is spent on freight transportation costs. It’s important to price shipping costs and form relationships with reliable vendors.
- Customer Expectations: Same-day delivery can place exceedingly high-pressure demands on companies who perhaps aren’t equipped to fulfill this consumer desire. Exceedingly rapid delivery, however, isn’t the only unique selling proposition available to companies.
- The Seven Rs: Companies consistently struggle to get the right product, to the right consumer, in the right quantity, in the right condition, at the right place, at the right time, and at the right cost.
How to Improve Outbound Logistics?
The key to improvement is utilizing technology, nurturing relationships, and artful negotiation.
- Understanding fast delivery: If you want to provide same-day delivery, you need to have the infrastructure in place to make it happen. Some distribution centers employ a lumper service, i.e., third-party workers, to load and unload trucks to speed up the process.
- Improve partner relationships: Working closely with freight shippers and retailers can provide you with valuable data to fine-tune production, order fulfillment, and shipping. Distributing business between a few carriers might provide greater control over price and service.
- Plan routes smartly: Planning efficient routes can reduce fuel costs, last-mile expenditure, and reduce waiting time, boosting customer satisfaction.
- Employ a 3PL: Third-party logistics providers often have the resources and expertise to offer discounts and better service. They also allow you to scale up or down without worrying about fleet or driver overheads.
Benefits of Optimizing the Outbound Logistics
Inbound logistics and outbound logistics are both critical for the successful supply chain management. Optimizing outbound logistics processes keeps your customers happy and saves you time and money as the supplier.
- Faster deliveries: Patience may be a virtue, but not when it comes to online orders. Customers today expect faster deliveries than ever before, so it’s never been more important to manage your routes and ensure quick, on-time deliveries.
- Reduced cancellations: Failed or incorrect deliveries can seriously hurt your business. By using the right technology to manage your outbound logistics, you can minimize these occurrences.
- Better transparency: Outbound logistics focuses on building your awareness of where an outbound delivery is at any given moment. Customer inquiries on when they can expect their package are no longer a thing to fear!
- Increase brand loyalty and customer satisfaction: Speedy deliveries make for happy customers! Well-designed outbound logistics processes will keep your customers coming back.
What's the Difference Between Inbound and Outbound Logistics?
What are inbound and outbound logistics, exactly? Both focus on the handling and transportation of goods. Below is a summary:
What Is Inbound and Outbound Logistics Software
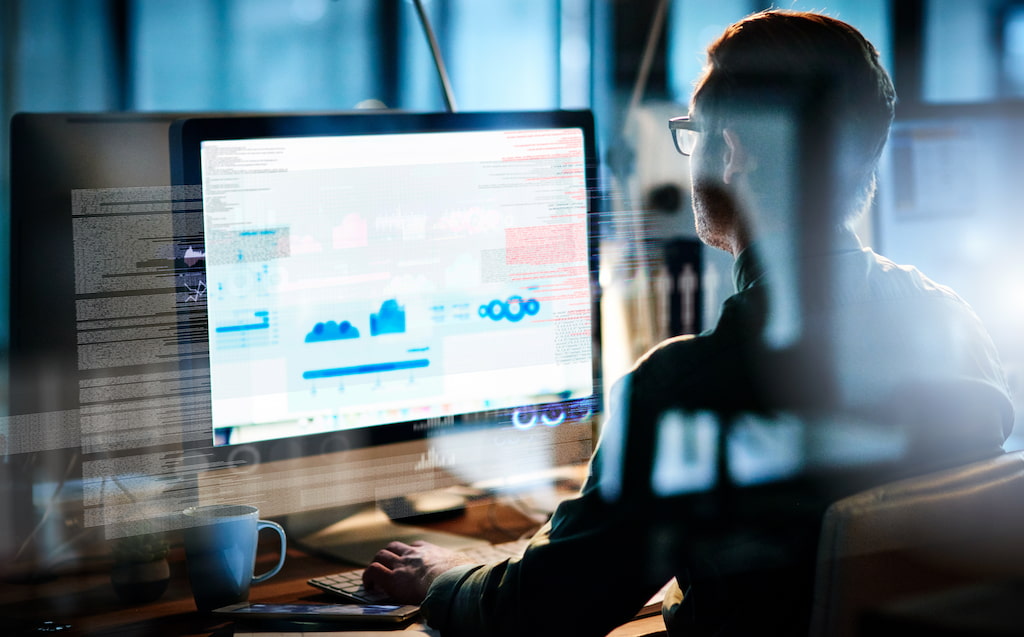
Utilizing inbound and outbound logistics software synchronizes both processes and enables smooth production. Today’s software can manage core financial processes, track inventory and customer orders, as well as carrier timetables and their freight capacity. Using AI processes to support advanced planning and real-time control accelerates logistics throughput and reduces inefficiencies.
Inbound and outbound logistics are tools for business growth and opportunities for cost savings. Specialized software reduces overheads and provides invaluable data, so businesses can make decisions based on facts. With the right software tools, a company remains agile and ready to tackle the fluctuating needs of consumers and supply chains.
Conclusion
The device you’re reading this on managed to get to you through a complex process; successful inbound and outbound logistics. Without it, companies wouldn’t make money, and consumers wouldn’t survive. Get a freight shipping quote if you’re interested in finding out how DFW trucking company can help you manage and optimize inbound logistics.
Inbound And Outbound Logistics FAQ
What is inbound logistics in a value chain?
This process refers to the influx of raw materials to manufacturing facilities. It is the first stage in the value chain and involves sourcing, storage, and distribution of materials, inventory tracking, and optimizing the movement of goods from suppliers to the manufacturing plant. It focuses on the supply part of the supply-demand equation.
How to calculate inbound logistics right?
Inbound logistics generally consume more than 40% of an organization’s annual freight budget, accumulating up to 5.% of a firm’s total annual sales, depending on the industry sector. Take your total sales revenue and subtract total production costs, then determine if the cost percentage falls within this ballpark.
What is outbound logistics in a value chain?
Outbound logistics involves the flow of finished products from a company to its customers. It focuses on the demand side of the supply-demand equation and involves storing and moving goods, order fulfillment, packing, shipping, delivery, and customer service related to delivery. It plays a critical role in a supplier’s overall customer relationship management process.